Applicazioni principali:
microturbine per cogenerazione funzionanti a fluido in pressione aria – aria calda – vapore – o fluido misto gas/liquido
dav
motori/mandrini pneumatici ad alta velocità per finiture, rettifiche, micro foratura, o microturbine per uso medicale.
In breve i vantaggi principali:
- Costo molto basso della macchina (statore e rotore ottenuti con chemical etching)
Lo statore a microugelli realizzato tramite il processo di fotoincisione e tranciatura garantisce una estrema precisione (qualità quasi fotografica) nella realizzazione della forma e orientamento dei passaggi del flusso indipendentemente dalle dimensioni micrometriche e dalla densità di questi.Il processo i tempi e i costi di lavorazione sono bassissimi e indipendenti dal materiale che si intende utilizzare (ottone, bronzo, rame, alluminio, acciaio inox AISI 304 3160 321 301, inconel, acciai uso chirurgico,ecc. ecc. )
Per la realizzazione delle parti rotore e statore non sono necessari utensili o macchine cnc. con conseguente notevole abbattimanto dei costi.
- Fluido di qualsiasi natura (insensibile all’impurità dell’aria di alimento e diametro massimo delle particelle solide trascinate dell’ordine dei passaggi degli ugelli statorici)
- Assenza di vibrazioni (non vi è l’alternanza pala/passaggio fluido)
- Usura molto bassa del rotore piochè la differenza tra le velocità fuido-rotore è bassa.
- La coppia è massima in avviamento, aumentando al diminuire della velocità
- Macchina modulare: la potenza (coppia) richiesta è ottenibile variando opportunamente il numero dei dischi rotorici in rapporto con le portate e pressioni del fluido disponibile.
- Insensibilità alle variazioni della pressione di alimento: il rendimento e la velocità massima sono ottenibili già con una pressione all’ingresso ugelli statorici di 1 bar relativo (2 bar assoluti)
La presente invenzione riferita al settore delle macchine a fluido (motrici od operatrici) dinamiche di piccola o piccolissima taglia, apporta un miglioramento delle prestazioni e dei costi di produzione mediante un nuovo approccio di progettazione e costruzione.
L’invenzione in particolare consiste in due step:
- cambio di filosofia di progettazione: si passa da un numero non elevato di passaggi di grande sezione al cui interno avvengono le trasformazioni termodinamiche, ad una macchina costituita anche da centinaia se non migliaia di passaggi con sezione quasi microscopica (macchina “porosa”).
- Cambio del modo in cui viene costruita la macchina: si passa da una concezione di lavorazioni da pieno ad una quasi-additiva in quanto si impilano un gran numero di lamine di forma diversa per ottenere la forma tridimensionale della macchina finita (macchina lamellare).
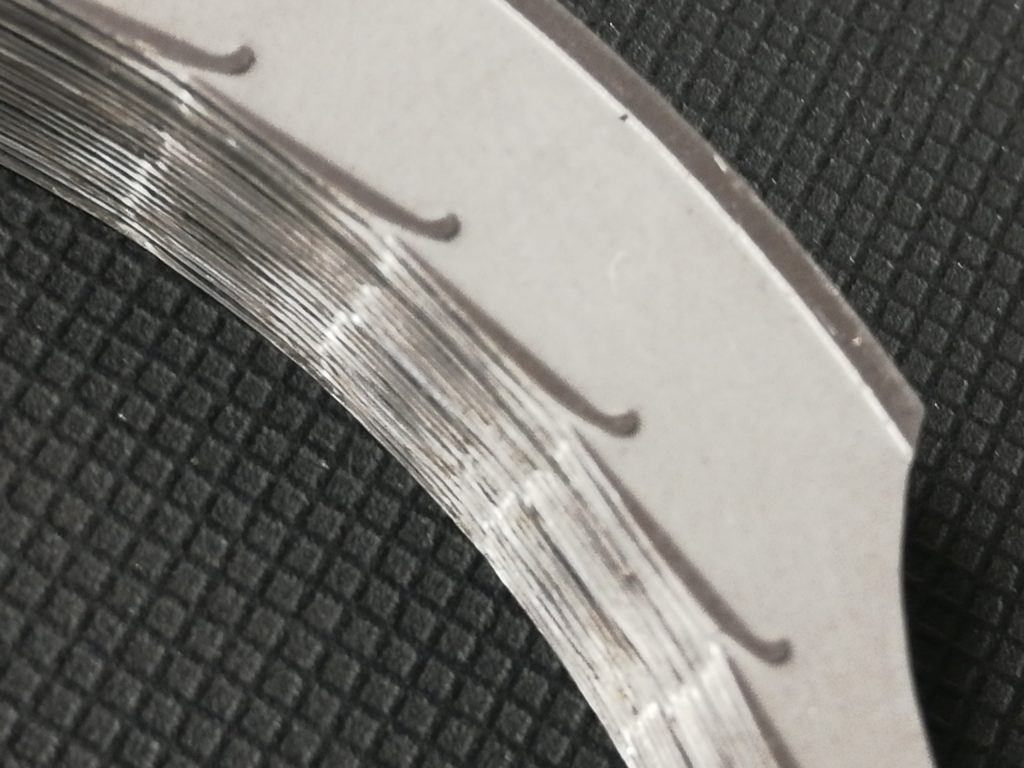
Stato dell’arte
Allo stato dell’arte sono note soluzioni per ottenere le trasformazioni termomeccaniche richieste in quanto nelle macchine a fluido dinamiche (sia motrici sia operatrici) si ha la trasformazione dell’energia contenuta in un fluido (entalpia) in energia meccanica e viceversa. Per ottenere queste trasformazioni è necessario che vi sia l’interazione tra il fluido ed un organo meccanico in movimento. Naturalmente tali trasformazioni avvengono solo se il fluido è opportunamente guidato attraverso ugelli (o palette) in modo da trasformare la sua entalpia in energia cinetica e quindi in forze e viceversa. La posizione degli ugelli (o palette) può essere indifferentemente sullo statore o sul rotore o su entrambe a seconda del tipo (grado di reazione) della macchina.
Nella maggior parte delle macchine di taglia piccola il numero degli ugelli (o palette) solitamente non supera la ventina, ciò comporta lungo lo sviluppo del confine rotore/statore una discretizzazione di tale confine in zone in cui c’è flusso e zone in cui non c’è in quanto parete: questa alternanza causa vortici e forti attriti sulle pareti in quanto la componente radiale della velocità non è nulla ed il gradiente della velocità stessa può raggiungere valori molto elevati, anche in questo caso con grosse perdite di rendimento. A causa di queste limitazioni, infatti, le macchine di piccola taglia sono sovente del tipo a reazione (la trasformazione entalpica avviene all’interno del rotore) proprio per evitare la formazione di molti vortici in ingresso al rotore, con una perdita significativa di potenza e rendimento.
Altro problema di queste macchine è la loro poca flessibilità a mutazioni delle specifiche richieste: una volta che si è costruita una macchina, tale macchina è un pezzo unico non modificabile, se vi è un cambiamento nelle specifiche che porta al fuori del campo operativo, occorre sostituire completamente la macchina. Inoltre è difficile trovare sul mercato la macchina che sposi perfettamente le richieste progettuali tranne che in rari casi.
Scopi dell’invenzione
Per risolvere i problemi presentati nel paragrafo precedente si è pensato ad una macchina in cui il flusso sia distribuito praticamente senza soluzioni di continuità lungo tutta la circonferenza di confine statore-rotore.
dav
L’idea principale di questo tipo di macchina è quella di distribuire le immissioni/ricezioni del fluido motrice lungo tutta la circonferenza di confine, in modo da rendere minimo lo strisciamento di esso sulle pareti e quindi cercare di limitare le perdite per attrito su parti non generanti lavoro, limitando al massimo le componenti della velocità non tangenti alle superfici.
Praticamente quasi tutto il confine statore-rotore è sede di passaggio del fluido motore. Naturalmente non è possibile ottenere la condizione limite di passaggio di fluido senza soluzione di continuità, anche perché è necessario direzionare il fluido. Perciò si cerca di fare i passaggi elaboranti il fluido il più piccoli possibile per minimizzare le fluttuazioni di pressione e velocità lungo la circonferenza di confine statore-rotore e limitare al massimo la lunghezza delle scie turbolente lasciate dalle pareti tra i passaggi del fluido.
Inoltre la portata elaborata dalla macchina è definita dal rotore e la presenza di un gran numero di ugelli statorici di dimensioni troppo elevate porta facilmente al choking dello stesso, causando la diminuzione del salto disponibile di pressione sugli ugelli ed una caduta del rendimento degli stessi.
Dall’unione di queste due idee si è arrivati a pensare ad uno statore “poroso”: uno statore in cui gli ugelli sono in numero molto rilevante (anche diverse centinaia) e di dimensioni molto piccole
La necessità di ridurre al minimo le dimensioni delle palette (o ugelli) porta però a diversi problemi:
- Primo tra tutti la necessità di mantenere la sezione di passaggio tra le palette tendente quanto più possibile alla forma circolare, per limitare al minimo la sezione bagnata dal fluido e quindi gli attriti.
- Limiti tecnologici delle lavorazioni convenzionali, in quanto non è possibile pensare di riuscire a fare passaggi troppo piccoli con lavorazioni meccaniche, anche non tenendo conto delle ovvie limitazioni di costo.
- Limitazioni nelle tempistiche di costruzione della macchina: uno statore di questo tipo deve contenere anche diverse centinaia di ugelli ed il tempo di lavorazione dal pieno di un numero così rilevante di passaggi non è accettabile. Anche pensando di costruire lo statore con tecnologie di tipo additivo (stampa 3d), le attuali tecnologie non permettono la costruzione dello statore con la necessaria precisione (i passaggi devono avere dimensione anche inferiore al decimo di millimetro) e sufficiente resistenza (sollecitazioni, temperature elevate del fluido).
Per superare questi problemi, si è pensato di costruire lo statore con un numero abbastanza elevato di lamine (layer).
Con tale sistema, a macchina già costruita, è inoltre possibile modificare a piacimento il numero delle lamine, la loro forma, la dimensione dei passaggi senza modificare il carter della macchina ed in maniera molto veloce e poco costosa, si ottiene cioè una macchina diversa in poco tempo e con poca spesa, senza disporre di grosse attrezzature.
In ogni singolo layer viene inciso la forma dell’ugello (o paletta) tramite fotoincisione chimica. Tale procedimento permette di ottenere precisioni impensabili rispetto ad altri tipi di lavorazioni meccaniche, il materiale fondamentalmente mantiene tutte le sue caratteristiche meccaniche, è un procedimento molto economico, veloce e poco costoso, adatto alla produzione in grande serie.
Inoltre in tale procedimento, facendo avvenire l’attacco chimico solo da un lato della lamina, si può ottenere direttamente la schiera di ugelli (palette) fissati ad una lamina di metà spessore, che è una struttura molto robusta impaccabile con semplicità per ottenere lo statore (rotore) con le richieste caratteristiche della sezione dei passaggi.